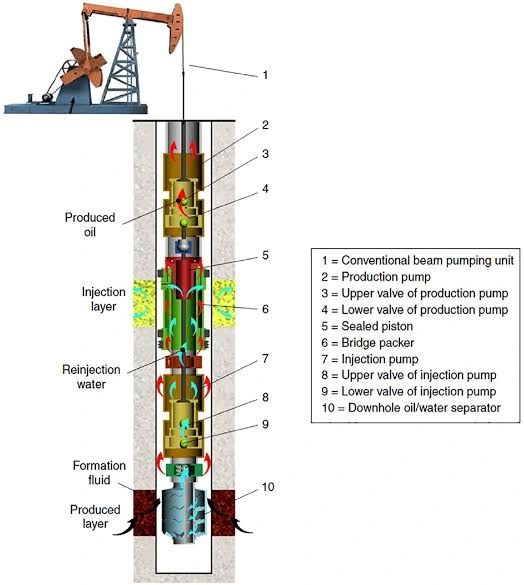
What is a Progressive Cavity Pump (PCP)?
A PCP is a positive displacement pump consisting of a helical rotor that rotates within a stator. The interaction between the rotor and stator creates sealed cavities that move fluid progressively from the pump’s intake to its discharge.
Key Components of a PCP
- Rotor:
A metallic, single-threaded helix that rotates to displace the fluid. - Stator:
A double-threaded helical cavity, usually made of elastomer, that encases the rotor. - Drive System:
Transfers rotational energy from the surface to the downhole pump. It typically includes a rod string and a surface drivehead. - Tubing and Production Casing:
Guides fluid from the pump to the surface.
Working Principle of PCPs
The PCP operates by forming continuous cavities between the rotor and stator. As the rotor turns:
- A cavity is created at the pump’s intake.
- Fluid is trapped in the cavity and moved upward as the rotor rotates.
- This process repeats continuously, delivering fluid to the surface in a smooth, non-pulsating flow.
Advantages of Progressive Cavity Pumps
- Versatility in Fluid Handling:
PCPs can efficiently pump a wide range of fluids, including heavy oil, water-oil mixtures, and fluids with high solids content. - Low Shear Rate:
The gentle pumping action minimizes emulsion formation, making PCPs suitable for sensitive fluids. - High Efficiency:
PCPs are highly efficient in low-production wells, providing steady and reliable flow rates. - Simple Design and Maintenance:
Fewer moving parts make PCPs easier to maintain and less prone to mechanical failure. - Energy Efficiency:
PCPs consume less energy compared to other artificial lift systems, such as beam pumps, for the same production rate. - Minimal Gas Interference:
PCPs can handle moderate amounts of gas without losing efficiency, reducing the need for gas separators.
Limitations of Progressive Cavity Pumps
- Temperature Sensitivity:
The elastomeric stator can degrade at high temperatures, limiting the use of PCPs in thermal recovery applications. - Solids Wear:
Although capable of handling solids, excessive abrasive particles can wear out the rotor and stator, reducing pump life. - Limited Depth Capability:
PCPs are less effective in wells with high depth due to torque and rod-string limitations. - High Initial Cost:
While maintenance is simpler, the upfront cost of PCP systems can be higher than other lift methods.